Sommaire:
Remerciement
Introduction
- La passionnante histoire de la bière
- Chronologie de la bière
- Fabrication
- Réalisation des bières de GEII
- Première bière: apprentissage de brassage
- Deuxième Bière: consommation d’énergie
- Automatisation
- liste du matériel nécessaire
- Motorisation du moulin
- motorisation du malaxeur
- Asservissement de température
- Amélioration possible
- Conclusion
Remerciements:
Ce projet n’aurait pu être réalisé sans l’aide d’une multitude de personnes que nous tenons à remercier ici. Parmi elles :
– M. Ould-Abdeslam pour la proposition et le suivi complet de ce projet ainsi que pour les commandes de matériel,
– les techniciens de l’IUT qui nous ont permis d’automatiser le moulin à l’aide d’une simple pièce qui nous manquait,
– M. De Sabatta pour sa patience et ses nombreux conseils,
– M. Hiebel, du lycée Charles de Gaulle à PULVERSHEIM, section “chaudronnerie”, pour la tôle en inox qui nous manquait afin de réaliser notre malaxeur.
Nous tenons également à remercier M. Drouaz qui nous a apporté des conseils pour la fabrication de la bière et qui était présent à chacun de nos brassages ainsi que pour les stérilisations du matériel, ainsi que toutes les personnes qui se sont démenées pour nous trouver des bouteilles de bières refermables ou qui peuvent être encapsulées.
Pour finir, nous remercions l’IUT qui nous a donné le financement pour aboutir et surtout commencer ce magnifique projet.
Introduction:
Nous sommes deux étudiantes de deuxième année en GEII: Toussaint Raphaëlle et Dusausay Laura.
Dans le cadre de notre scolarité, nous avons choisi, dans notre projet, de créer une microbrasserie, dont l’automatisation exploite l’énergie solaire.
Mais dans un premier temps, laissez-nous vous faire découvrir cet art ancestral à travers son histoire, sa fabrication ainsi que son automatisation.
1.La passionnante histoire de la bière :
1. Chronologie de la bière
Le principe de la bière est de réaliser une fermentation de céréales. La première a vu le jour à Jericho (à côté de Jérusalem) en 12 000 avant J.C.
Celui-ci s’est développé partout dans le monde en faisant évoluer sa recette de siècle en siècle.
En 4 000 av JC, en Egypte, la bière était une boisson divine. Plus tard elle gagnera l’Europe en devenant une boisson remplie de vertus médicinales. En 1435 ce sont les prêtres qui ont l’exclusivité de la fabrication de ce breuvage. Puis durant l’ère industrielle Pasteur va faire la découverte de la levure ce qui va révolutionner le mode de préparation. Finalement ce n’est qu’en 1950 que la bière va commencer à être industrialisée.
1.2 Fabrication
1.2.1 Matières premières
Eau |
Il faut 6L à 8L pour 1L de bière |
malt |
Orge germé et caramélisé, froment, ou seigle |
houblon |
Pour l’amertume, l’arôme, aseptisation, digestibilité |
levure |
Pour la fermentation alcoolique |
Tab 1: Les matières premières de la bière
1.2.2 Les 5 grandes étapes
maltage |
Le malt crée les enzymes nécessaires à la création d’alcool lors de la fermentation (déjà fait lors de la commande du malt) |
Le brassage |
On hydrate et chauffe le malt permettant l’activation des enzymes ainsi que l’obtention des sucres |
cuisson du moût |
On filtre la fermentation. Le liquide qui en ressort est chauffé à plusieurs températures avec du houblon et d’autres épices. Cette étape permet de donner du goût à la bière |
fermentation |
Cela désigne la réaction chimique qui transforme le sucre en alcool. L’ajout de levure permet de gérer ce procédé.Celui-ci est fait en 2 temps de repos avec des températures différentes. |
la garde |
Procédé de la gazéification |
|
|
Tab 2: Explication des procédés de fabrication
2.Réalisation des bières de GEII
2.1 Première Bière: apprentissage de brassage
Pour notre projet nous avons commandé une microbrasserie afin de l’automatiser. Mais avant toute chose il fallait que l’on se familiarise avec les différents procédés pour connaître les étapes essentielles à automatiser.
Nous voilà donc parties dans la création de notre Première bière.
2.1.1 Matériel et matières premières
Pour 20L de bière:
Kit Brewferm; Une balance; Un minuteur; Récipient pour le malt concassé; Rallonge électrique; Cotons tiges pour stériliser le robinet des cuves
4,4 kg de malt du kit Brewferm; Houblon du kit Brewferm; Eau (suffisamment pour les différentes phases de cuisson et le refroidissement); Sucre Candy du kit Brewferm; Levure du kit Brewferm
2.1.2 Recette de fabrication
Pour commencer, moudre le malt à l’aide du moulin.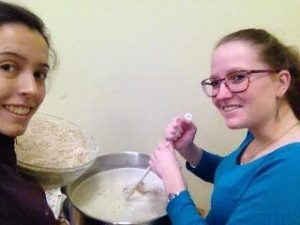
Faire chauffer 20 L d’eau jusqu’à atteindre 52°C. Puis ajouter le malt. Après 15 minutes de cuisson, augmenter la température à 62°C puis attendre 45 minutes. Augmenter la température jusqu’à 72°C puis laisser cuire 15 minutes. Enfin, augmenter la température jusqu’à 78°C et attendre 5 minutes. La phase d’empâtage est terminée, on peut passer à la filtration.
Mettre le contenu de la cuve dans une cuve de filtration puis récupérer le liquide sortant du robinet qu’on remet à nouveau dans la cuve de filtration jusqu’à ce que le liquide devienne plus clair.
Vider le contenu de la cuve par le robinet dans la cuve chauffante jusqu’à atteindre 24 L. Pour cela, ajouter de l’eau à la température de 75°C dans la cuve de filtration et patienter. Une fois la valeur de 24L atteinte, faire chauffer jusqu’à atteindre l’ébullition. Une fois le mélange porté à ébullition mettre la chaussette contenant le houblon et patienter pendant 80 minutes.
Commencer à stériliser le refroidisseur, la cuillère ainsi que la cuve de fermentation.
ATTENTION : une fois stérilisé, il ne faut plus mettre ce matériel en contact avec autre chose que la future bière.
A la fin des 80 minutes de cuisson, enlever la chaussette et passer à la phase de refroidissement.
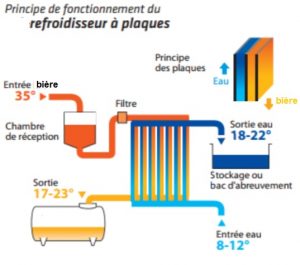
Brancher un tuyau entre le robinet de la cuve chauffante et le refroidisseur, un tuyau entre le refroidisseur et la cuve de fermentation, brancher un tuyau entre le refroidisseur et le robinet d’eau froide et le dernier tuyau entre le refroidisseur et l’évier dans lequel ressortira l’eau qui sera chaude. Activer l’eau froide avec un gros flux puis ouvrir le robinet de la cuve chauffante pour libérer la bière. Attendre que le processus soit terminé.
Pour terminer, ajouter la levure dans de l’eau suivant les indications de la levure. Ajouter cette levure dans la bière et mélanger sans faire de bulle.
Enfin fermer la cuve de fermentation et ajouter le barboteur, dans celui-ci, mettre un peu d’eau.
ATTENTION : l’eau ne doit pas entrer en contact avec la bière.
Mettre la cuve de fermentation dans une salle à 20°C pendant 2 semaines. Après 2 semaines de fermentation, mettre la cuve dans une salle/cave à 15°C pendant 2 semaines.
Stériliser les bouteilles qui vont contenir la bière 48h avant la mise en bouteille à l’aide de chemipro dilué dans de l’eau. Le jour de la mise en bouteille, faire fondre avec de l’eau 7g/L de sucre puis l’ajouter dans la cuve de fermentation (après avoir stérilisé la cuillère).
Stériliser le robinet de la cuve de fermentation. Mettre les bouteilles stérilisées 10 minutes dans de l’eau bouillante puis mettre la bière dans les bouteilles. Stériliser les capsules et capsuler les bouteilles.
Laisser la bière minimum 2 semaines en bouteilles à température ambiante avant dégustation.
2.2 Deuxième Bière : consommation d’énergie
Début juin 2018 l’IUT de Mulhouse a investi dans 2 panneaux solaires. Ils peuvent produire jusqu’à 2,2 kWh.
Fonctionnement d’un panneau solaire:
Un panneau solaire est constitué de cellules dites photovoltaïque. Une cellule est constituée de 2 couches de silicium dopées respectivement P et N. Initialement, cette jonction PN est électriquement neutre. Un photon d’énergie suffisante va créer un trou par arrachement d’un l’électron. Par l’agitation des électrons voisins, ce trou va être comblé en piégeant un électron. À l’échelle de la cellule, le comportement est équivalent à une force électromotrice. Si la jonction est insérée dans un circuit fermé, un courant va circuler. Pour augmenter la puissance disponible, il faut placer plusieurs cellules pour former un panneau solaire. La tension est continue. L’énergie peut alors être stockée dans une batterie, qui joue le rôle de récepteur quand elle se charge, puis de générateur lorsqu’elle débite vers un utilisateur. Si l’utilisateur exploite une tension sinusoïdale, il faut alors intercaler un onduleur.
Lors de l’installation il faut veiller qu’aucun objet faisant de l’ombre soit à proximité du panneau. En effet contre toute attente, lorsqu’une cellule est ombragée, c’est la totalité du panneau qui cesse de produire. Ainsi, à l’IUT, un arbre cache une partie du panneau et fait perdre 30% de la production.
Lors de la première bière nous n’avons pas pu mesurer la consommation d’énergie dont nous avons besoin lors de la fabrication. C’est lors de la fabrication d’une seconde bière, dont la recette est en annexes 2 et 3, que nous avons mesuré la consommation d’énergie nécessaire. Toute les données de production des panneaux solaire de l’IUT sont envoyées sur la plateforme.
Ainsi nous avons pu voir notre consommation d’énergie.
Lors de la fabrication de cette bière, nous avons mesuré la consommation électrique de tout le processus en utilisant les batteries (stock maximal de 4,8 kWh). Ces batteries conservent l’énergie récupérée grâce au panneau solaire installé à l’extérieur du bâtiment. Nous nous baserons sur la consommation des batteries pour ultérieurement faire une analyse de la consommation d’énergie totale d’un brassage.
Au début du processus les batteries étaient chargées à 89% de la charge maximale. On a fait chauffer de l’eau jusqu’à 80°C avant de la laisser refroidir à 67°C. Une fois à 80°C les batteries étaient à 72% de leur charge maximale. Juste avant la phase de filtration les batteries étaient à 68%. Puis on fait chauffer de l’eau de rinçage, une fois l’eau à 78°C les batteries étaient à 60%. Puis on porte l’eau à ébullition. Au début des 80 minutes de cuisson les batteries étaient à 43% puis à la fin de la cuisson elles étaient à 26%.
Remarque: Lors de cette journée les batteries ont pu se recharger légèrement.
Nous voyons sur la courbe de production des batteries ci-dessus, que de 10 h à 11 h 30 le panneau a produit une puissance jusqu’à 600 W et de 15 h 30 à 16 h la consommation était moindre (cf les encadrés noirs de la Fig 8)
Au bilan, pour faire tout le processus (sans compter la mise en bouteille) on a utilisé 89 % – 26 % = 63 % des batteries. Soit 0,63 x 4,8 kWh = 3 kWh. En toute rigueur, on a remarqué que lors de cette journée, les batteries ont pu se recharger légèrement, ce qui signifie que l’énergie réelle consommée est légèrement supérieure.
Cet essai a montré la faisabilité d’alimenter notre installation par le réseau issu des panneaux solaire.
3. Automatisation :
3.1 Liste du matériel nécessaire :
pour le malaxeur et le moulin |
Pour le PID de la cuve |
Une perceuse 900W/230V |
Une carte Raspberry Pi avec son écran tactile, son alimentation et une carte SD |
Des boulot M6 et M8 en inox |
Un clavier, souris |
Une tige filetée M6 en inox d’une longueure d’un mètre
Une tige filetée M8 en inox d’une longueure d’un mètre |
Une LED de roue libre 1N4002 |
Un fer plat en inox |
une sonde PT100 |
|
Pour la sécurité:
Un transformateur 12V 500mA
Un relais de puissance 12V 300mA
Un relais 5V
Une multiprise et une prise terre |
Une carte Arduino Uno avec son câble et une résistance 100 Ohm |
3.2 Motorisation du moulin :
Lors de la fabrication de la deuxième bière, nous avons motorisé la rotation du moulin à malt. Pour cela les techniciens de l’IUT nous ont usiné une pièce s’adaptant directement au moulinet du moulin pour ainsi utiliser une perceuse.
La motorisation du moulin est terminée.
3.3 Motorisation du malaxeur :
Nous avons décidé de créer une pièce totalement en inox pour mélanger la bière de façon autonome.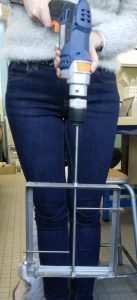
Le choix de l’inox n’est pas anodin: c’est le seul métal inoxydable, adapté à l’alimentaire, et sans influence sur la saveur de la bière.
De ce fait nous avons réalisé un carré avec un fer plat d’un mètre où nous avons inséré des tiges filetées.
De ce fait lors de la rotation fait par la perceuse le liquide dans la cuve est mélangé de façon homogène.
3.4 Asservissement de la température :
Afin d’asservir la température, nous avons utilisé une sonde PT100, une carte Arduino Uno, une carte Raspberry Pi, un écran, un relais 5V, un relais 12V, un transformateur, une prise avec terre et la cuve chauffante Brewferm.
Le but est de commander la sonde PT100 à l’aide d’un Raspberry Pi afin que la température soit affichée sur un écran et qu’elle se régule seule suivant le programme de cuisson demandé. La sonde PT100 envoie un signal analogique et le Raspberry Pi ne reçoit que des signaux numériques, c’est pourquoi on ajoute une carte Arduino Uno qui fait office de convertisseur analogique/numérique. La carte Raspberry Pi sera donc reliée à un écran qui affichera le programme de cuisson et la température.
Elle sera aussi reliée à un relais 5V qui sera relié à un relais de puissance 12V. Les deux relais servent de protection à notre matériel. Ce relais de puissance sera relié d’un côté par la cuve chauffante Brewferm, et d’un autre côté par un transformateur qui sera branché au 230V de la prise secteur.
Nous avons choisi la sonde PT100 grâce à ses caractéristiques :
– une précision d’un dixième de degré : largement suffisant pour notre application,
– gamme de température allant de 0 °C à 100 °C : adaptée à notre température de cuisson qui est de 90 °C,
– temps de réponse inférieure à 1 s : parfaitement cohérent avec notre projet. En effet, la montée en température de notre cuve est environ de 30 minutes pour une élévation de 20 °C. Le temps de réponse du capteur seul est donc négligeable.
3.4.1 Connectique Raspberry Pi → Cuve
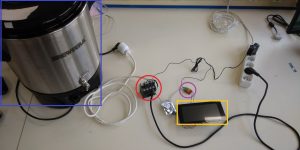
cuve relais de puissance relais 5V Raspy
Pour s’assurer de la sécurité de la cuve ainsi que de l’interface, nous utilisons des relais.
On va utiliser une triplette avec un arrêt ON/OFF de plus de 3000W pour s’assurer qu’elle supporte les 2000W de la cuve, la perceuse du malaxeur ainsi que les relais.
Par loi de Joule, 2kW, 230 V aboutit à un courant de 8,7 A. Ce qui nécessite un câble de section 1 mm2. Une fois le branchement réalisé nous pouvons passer à la programmation.
3.4.2 Programmation de la sonde:
Objectif : à travers une interface l’utilisateur choisira les 3 temps de cuisson et les températures associées ainsi que le temps de houblon. De cette façon l’utilisateur peut vaquer à ses occupations en recevant un email à chaque changement de cuisson, pour chaque houblon et fin de cuisson.
Nous avons donc commencé cette partie de l’automatisation par la programmation de la carte Raspberry Pi et de la carte Arduino Uno. La particularité de la sonde PT100, c’est qu’à 0 degrés Celsius celle-ci agit comme une résistance de 100 ohms. Celle-ci est reliée à la carte Arduino à l’aide d’un pont diviseur de tension avec une résistance 100 Ohm afin de faire la conversion analogique/numérique et de sortir une valeur de la température. (Fig 13) Cette valeur de température sera ensuite envoyée au Raspberry Pi. Le Raspberry Pi sera programmé pour recevoir les informations de la sonde dans un premier temps.
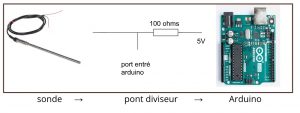
Pour l’arduino nous avons fait un programme nous permet de récupérer les valeurs de la sonde qui arrivent sur le port analogique de l’Arduino. Nous recevons les valeurs en millivolts que nous convertissons en degrés Celsius.
Pour ce faire, nous utilisons la fonction map qui permet de faire cette conversion. Pour calibrer la sonde, nous la mettons à 0°C et récupérons la valeur en millivolt. Nous ferons de même pour 100°C. Pour finir nous affichons le résultat en degrés sur la console.
3.4.3 Programmation du contrôle de la cuve
Nous allons utiliser le logiciel python pour programmer la cuve. Le principe de fonctionnement est le suivant :
- Nous contrôlons constamment la température, si elle est trop froide on active le GPIO 12 (pin sur lequel est branché la cuve) donc on allume la cuve, sinon on le désactive pour l’éteindre.
- Nous avons créé des paliers de température et de houblons
- Nous utilisons des minuteurs pour savoir si le temps des paliers sont écoulés pour passer au suivant
- Nous pilotons également 5 autres GPIO qui vont servir à envoyer des mails de suivi à l’utilisateur
Initialisation :
En début de programme toutes les variables, mettrons les GPIO sur FALSE (éteint), nous enregistrons les temps de cuisson et des houblons saisis
Chronomètre:
Nous utilisons le temps instantané sur lequel nous allons ajouter la durée saisie par l’utilisateur.
Cependant l’utilisateur rentre dans l’interface une durée en minute uniquement, telle que 90 minutes. Ainsi, nous avons créé 2 fonctions permettant de transformer et d’ajouter la saisie des minutes de l’utilisateur, en heure et minute d’arrivée.
ex: il est 13h30, nous saisissons 70 min → 70 minutes c’est 1h et 10 minutes.–> la fonction renvoie heure prévu= 1h, Minute prévu=40
Régulation de la température:
Pour cela, nous avons créé une fonction qui va piloter le GPIO relié à la cuve pour l’activer ou non. Le principe est le suivant : si la température reçue par la sonde est inférieure à la température désirée, on allume la cuve sinon on l’éteint.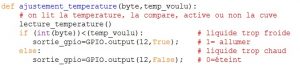
Architecture du programme:
Le programme est essentiellement constitué de “while” et de condition ”if”. Pour la première cuisson nous attendons que l’utilisateur lance le programme en appuyant sur le bouton de l’interface. Le programme est fait en deux parties : première cuisson et deuxième cuisson. A chaque fois nous devons attendre que l’utilisateur active la cuisson pour lancer l’algorithme.
Dès lors, pour la première cuisson, nous allons créer des boucles qui vont s’exécuter tant que la cuisson avec ses paliers ne sont pas arrivées à termes. A l’intérieur nous y plaçons la condition suivante :
Si la température relevé par la sonde est inférieure ou supérieure à 5°C de la température voulue pour le palier, nous la régulons comme nous avons vu précédemment.
Sinon nous lançons le chronomètre adéquat au palier. Et rentrons dans une boucle “tant que l’heure instantanée est inférieure à l’heure de fin du chronomètre” , nous relevons la température de la sonde, nous ajustons en conséquence la température et nous relevons l’heure instantanée. Dès qu’on sort du “tant que” nous activons le GPIO adapté pour envoyer un mail puis nous le remettons en état OFF.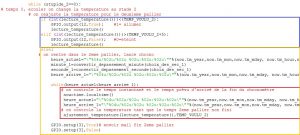
Cette condition va être répétée 3 fois soit le nombre de paliers maximum dans la première cuisson.
Lorsque les 3 paliers ont été exécutés, nous envoyons un mail de fin de première cuisson, sortons de tous les “tant que”, et coupons la cuve.
Pour la deuxième cuisson le principe est similaire mais simplifié car la température reste constante à 90°C.
Ainsi nous allons faire une série de chronomètre avec comme consigne tant que le chronomètre précédent n’est pas écoulé on ne passe pas au suivant. Dès qu’un chronomètre est écoulé nous envoyons un mail, indiquant qu’il faut rajouter un houblon.
3.4.4 Programmation de NodeRed
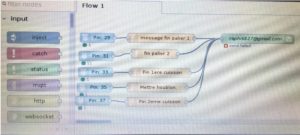
L’application Node Red se fait en trois étapes distinctes, nous commençons par détecter un changement de front sur l’un des pins du Raspberry Pi (boite bleue). Ce changement de front nous indiquera à quel moment de la cuisson nous nous situons. Ensuite, suivant le pin détecté, on fait une fonction dans laquelle on affiche le message voulu (boite orange). Pour finir, ce message est envoyé par email afin de prévenir l’utilisateur du changement de température dans une cuisson ou alors pour prévenir qu’il faut mettre le houblon (boite verte).
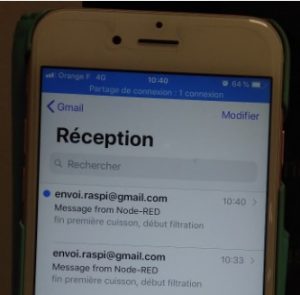
3.4.5 Programmation de l’interface
Voici l’interface utilisée: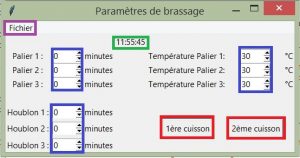
La programmation de l’interface se fait plutôt facilement. Il suffit de connaître les lignes de codes qui permettent de faire apparaître un bouton, une liste ou encore un texte et le tour est joué.
Voici des extraits de codes expliqués:
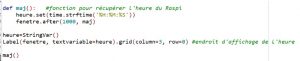
Nous avons choisi d’afficher l’heure sur l’interface afin de nous éviter d’avoir une montre à côté de nous. Pour cela, nous avons créé une fonction qui permet de récupérer l’heure instantanée du Raspberry Pi. Puis on sélectionne l’endroit où l’on veut l’affiche à l’aide de la fonction “.grid”. On choisit la colonne et la ligne dans lesquelles on veut que l’heure s’affiche.
Ensuite nous avons différentes zones de textes, ce sont les zones dans lesquelles on a déjà un texte comme “Palier 1”. Pour cela, nous utilisons un “Label”, nous lui donnons un nom et le plaçons dans l’interface toujours à l’aide de la fonction “.grid”.
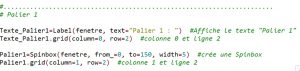
Nous avons également créé des “Spinbox” qui représentent les cases dans lesquelles nous choisissons une valeur. Nous décidons de pouvoir avoir des valeurs entre 0 et 150 “from_=0, to=150”, sauf pour la température que nous décidons d’avoir comme minimum 30 (from_=30, to=150). Les trois quarts du programme sont constitués de ces quatre lignes.
Pour terminer, nous avons ajouté deux boutons : un qui lancera le chronomètre de la première cuisson, et un qui lancera le chronomètre de la deuxième cuisson.

On utilise donc la fonction “Button” dans laquelle nous entrons un texte, qui figurera sur le bouton, ainsi qu’une commande à lancer et sa position dans l’interface. Cette commande se trouve dans le programme qui contrôle la cuve. Ainsi, lors de l’appui sur le bouton de l’interface, le chronomètre ainsi que les fonctions de chauffe se mettent en route grâce à la liaison entre les deux programmes.
Le petit plus de notre interface est d’avoir une barre de menu dans lequel nous avons un seul menu, “Fichier”.
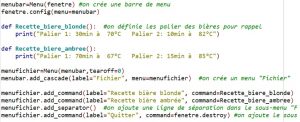
Dans ce menu “Fichier” nous avons créé un sous-menu “Bière blonde” et un sous-menu “Bière Ambrée”. En cliquant sur ces sous-menus, la recette de la bière s’affiche dans la console grâce à la fonction “command=”. Les fonctions “Recette_biere_blonde” et “Recette_biere_ambree” nous permettent tout simplement d’écrire dans la console le texte voulu qui est entre guillemets. Nous avons également ajouté un sous-menu “Quitter” qui permet de fermer l’interface.
4.Améliorations possibles :
Pour améliorer ce projet nous pouvons y apporter certaines modifications au niveau de la programmation, du malaxeur ou encore de la sonde.
4.1 La programmation:
Faute de temps, nous n’avons pas pu rassembler les programmes de l’interface et du programme principal. Pour les rassembler il y a 2 solutions. La première c’est de les rassembler tout en gardant 2 programmes différents, un pour le programme principal et un pour le programme de l’interface. La deuxième solution est de mettre les 2 programmes dans un seul et même programme qui lancera tout en même temps, cependant cette solution donnera un programme très long et assez complexe.
4.2 Le malaxeur:
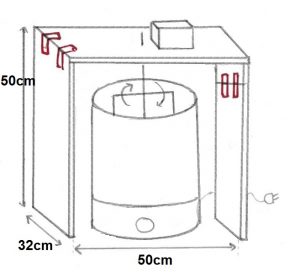
Le malaxeur est prêt mais il n’est pas en place. Pour cela, il faudrait faire un trou dans le couvercle de la cuve afin d’y faire passer la tige filetée qui se logera dans le mandrin de la perceuse. Mais pour tenir la perceuse il faudrait aussi pouvoir
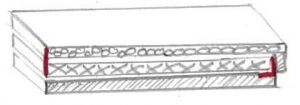
4.3 La sonde:
La sonde est programmée mais pour l’instant elle est juste posée dans la cuve. Pour la fixer, il faudrait faire un trou dans le couvercle de la cuve afin d’y faire passer la sonde, mais attention, il faudrait trouver une solution afin qu’elle ne soit pas emportée par le remous du malaxeur.
5. Conclusion
Ce projet fut très enrichissant que ce soit d‘un point de vue technique que d’un point de vue humain. En effet à travers ce projet nous avons pu rencontrer plusieurs personnes qui nous ont soutenu et partagé leurs savoirs.
Sur le côté technique, l’automatisation de la micro brasserie fut très complet. Nous avons vu la programmation sur 3 supports différents (Raspberry Pi, Node Red, Arduino). Pour la mécanique nous avons pensé, découpé, plié, assemblé différentes pièces. Côté électronique, nous nous sommes occupées des commandes et de l’assemblage des éléments.
La partie énergie nous a sensibilisé au fonctionnement et à la lecture des graphiques fournis par le panneau solaire.
Finalement, ce projet est bien plus qu’un simple projet brassage. C’est un assemblage de savoir faire que nous avons mené à bien grâce à nos connaissances et au partage des savoir-faire. Pour le mener à terme, nous n’avons pas hésité à prendre de notre temps personnel.
Malgré les difficultés rencontrées nous avons réussi à obtenir un système qui fonctionne convenablement.