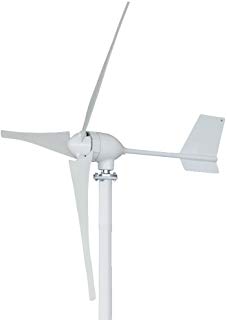
Remerciements
Nous souhaitons dans un premier temps remercier l’IUT de Mulhouse, pour nous avoir permis de réaliser ce projet.
Nous remercions également tous nos professeurs pour les connaissances qu’ils nous ont transmis durant ces deux années de DUT GEII et tout particulièrement M.Steger ainsi que M.Cudel pour l’accompagnement dont nous avons bénéficié tout au long de la réalisation de ce projet.
Enfin nous remercions nos camarades pour leur aide lors de la rédaction de ce rapport.
Membres du projet :
- Guilhem LEMAIRE
- Loïc SCHMITT
- Louise RIEFFEL
Sommaire
- Présentation du projet
- Analyse fonctionnelle
- Éolienne HY-600
- Equipements sélectionnés
- Dimensionnement des câbles
1. Présentation du projet
Dans le cadre d’un projet GEII, nous devions remettre en fonctionnement une éolienne pour l’IUT de Mulhouse. L’éolienne sur laquelle nous devions travailler était destinée à la casse suite à la démolition du site sur laquelle elle était installée, mais a été récupérée par l’IUT pour pouvoir la réutiliser. Malheureusement des parties étaient manquantes. L’IUT a pu récupérer uniquement la structure de l’éolienne, il nous faut alors reconstituer toute la partie électrique allant de pair avec l’éolienne. Nous disposons donc des pales, du moteur de l’éolienne, ainsi que de son mat.
2. Analyse fonctionnelle
Problématique : Réhabiliter et installer une éolienne sur le site de l’IUT de Mulhouse.
Ce diagramme répond au besoin en 3 questions : A qui ? / Sur quoi ? / Dans quel but ?
L’intérêt d’une éolienne est de transformer l’énergie cinétique du vent en une énergie électrique :
Schéma explicatif des composants d’une éolienne :
Fonctionnement souhaité de l’éolienne : L’éolienne génère de l’énergie électrique, cette énergie est ensuite transmise au contrôleur qui (?), l’énergie est ensuite stockée dans la batterie. L’onduleur est lui raccordé à la batterie ainsi qu’au réseau électrique. Si il reste de l’électricité dans la batterie, l’onduleur transfert cette électricité au réseau électrique de l’IUT, sinon il transfert à l’IUT l’énergie provenant du réseau électrique général.
Il nous fallait alors trouver les équipements suivants :
- Contrôleur -> Régulateur de charge
- Batterie
- Onduleur
- Connecteur de charge (celui initialement présent dans l’éolienne était défectueux)
3. Éolienne HY-600
Avec la référence trouvée sur l’éolienne nous avons pu trouver les documentations suivantes :
- Phaesun : Small ind Turbie User Manual HY-400, HY-600, HY-1000
- Windmax : Wind Turbine Guidbook HY-400, HY-600, HY-1000, HY-2000, HY-3000
Nous ne pouvons pas être sûrs qu’une de ces documentation correspond parfaitement à l’éolienne que nous disposons mais elles apportent des informations intéressantes qui nous serons plus qu’utiles pour la suite du projet.
On relève alors les informations issues des diverses documentations :
- Plus la vitesse moyenne du vent est élevée, plus l’éolienne sera génératrice d’énergie. La puissance disponible dans le vent augmente avec le cube de la vitesse du vent. Une turbulence plus faible entraîne également plus de puissance.
- Les obstacles (arbres, bâtiments, etc.) réduiront la vitesse du vent et, par conséquent, dégraderont les performances de l’éolienne. Une tour immédiatement sous le vent d’un bâtiment doit avoir au moins deux fois sa hauteur.
- Un dimensionnement correct des fils est important pour la sécurité et l’efficacité énergétique. Des câbles sous-dimensionnés entraîneront une perte d’énergie dans le système, créeront une surchauffe et augmenteront le risque d’incendie. Plus la taille du fil est grande, plus la perte d’énergie est faible. Cependant, les câbles de plus grande taille sont plus coûteux.
4. Equipements sélectionnés
Régulateur de charge
Nous avons choisi un régulateur de charge capable de charger des batteries 12/24V, qui fonctionne en mode standard (régulateur d’éolienne seule) ou en mode hybride (éolienne/solaire). La puissance de cet équipement est à 600w car c’est la puissance crête produite par notre éolienne.
Pour l’instant on souhaite utiliser cet équipement en mode standard, mais la perspective du mode hybride est une bonne chose pour permettre, dans le futur, la modification et/ou l’amélioration du système actuellement souhaité.
Batteries
Recherche de deux batteries correspondant aux caractéristiques du régulateur de charge :
Fonctionnement des batteries selon leur assemblage:
On dispose les batteries en série pour additionner les tensions et obtenir une tension de sortie de 24V.
On obtient alors les caractéristiques suivantes :
- Une puissance de 600W
- Une tension de 24V
- Un courant de : 600/24 =25A
- Une capacité de 75Ah ou de 50Ah, selon le modèle de batterie choisi
5. Dimensionnement des câbles
De l’éolienne au régulateur
Nous avons 40 mètres qui séparent l’éolienne du régulateur.
Ayant une puissance P = 600W et une tension U = 24V on en déduit la relation P = U*I*√3
D’où : I =P/(U∗√3) =600/(24∗√3) ≈ 15A
Chute de tension pour : S = 10 mm² et L = 40m
Chute de tension pour : S = 16 mm² et L = 40m
Un câble d’une section de 16mm² garantissait une plus faible chute de tension, mais après réflexion, en fonction de nos besoin et pour des raisons budgétaires, on choisira un câble de section 10mm².
D’après les caractéristiques ci-dessus nous avons choisi le câble suivant :
Du régulateur à la batterie
10 mètres séparent le régulateur des batteries.
A la sortie du régulateur nous avons une puissance P = 600W et une tension U = 24V
D’où I = P/U =600/24 ≈ 25A
Chute de tension pour : S = 6 mm² et L = 10m
Sachant qu’en sortie du régulateur nous sommes en monophasé, nous avons choisi les deux câbles suivants :
Cosse batterie + Embout de câble 6mm²
Du côté du régulateur le câblage se fera à l’aide d’embouts, du coté de la batterie le câblage se fera à partir de cosses à oeillet.
Du régulateur à l’onduleur
10 mètres séparent le régulateur de l’onduleur. A la sortie du régulateur nous avons une puissance P = 600W et une tension U = 24V
D’où I = P/U =600/24 ≈ 25A
Chute de tension pour : S = 6 mm² et L = 10m
Sachant qu’en sortie du régulateur nous sommes en monophasé, nous avons choisi les deux câbles suivants :
De l’onduleur au réseau IUT
Sachant qu’en sortie de l’onduleur nous sommes en triphasé, nous avons choisi le câble suivant :
Liaisons équipotentielles
30 mètres séparent l’éolienne du point de terre, on pourrait prendre une section similaire à celle du câble de l’éolienne jusqu’au régulateur mais pour question de sécurité on prendra du 16mm²
Ci dessous le câble choisi :
Choix de la cosse :
On a choisi de percer le mât afin de pouvoir y fixer le câble de mise à la terre à l’aide de cosses.
Conclusion
Fin mars/début avril nous avons eu la responsabilité de remettre en état une éolienne qui allait partir à la casse. La structure était conservée, mais la partie électrique de l’installation n’a pu être récupérée.Il nous fallait donc reconstituer cette partie.
Nous avons alors effectuer des recherches sur les différents équipements à intégrer afin de reconstituer l’installation.
Nous avons alors pu identifier et commander les équipements de base nécessaires au fonctionnement du système souhaité :
- Contrôleur
- Batterie
- Câbles
Il ne reste plus qu’à trouver l’onduleur et connecteur de charge qui assurera la liaison entre le moteur et le régulateur ainsi que toute la partie concernant la protection de l’ouvrage.
Webographie
Image principale éolienne :https://www.amazon.fr/TOPQSC-R%C3%A9sidentiel-Imperm%C3%A9able-D%C3%A9marrage-Efficacit%C3%A9/dp/B071QWM9RX/ref=sr_1_28?keywords=Mini+eolienne&qid=1560246280&s=gateway&sr=8-28
Image éolienne schéma : <a href=https://fr.pngtree.com>Graphiques de pngtree.com</a>
Schéma explicatif composants éolienne : https://www.connaissancedesenergies.org/quels-sont-les-constituants-d-une-eolienne-130125
Régulateur de charge : https://www.future-tech.fr/regulateur-de-charge-solaire-eolienne-12v-24v-600w,fr,4,757.cfm
Batterie 75Ah : https://fr.rs-online.com/web/p/batteries-au-plomb/7270439/
Batterie 50Ah : https://fr.rs-online.com/web/p/batteries-au-plomb/8720096/