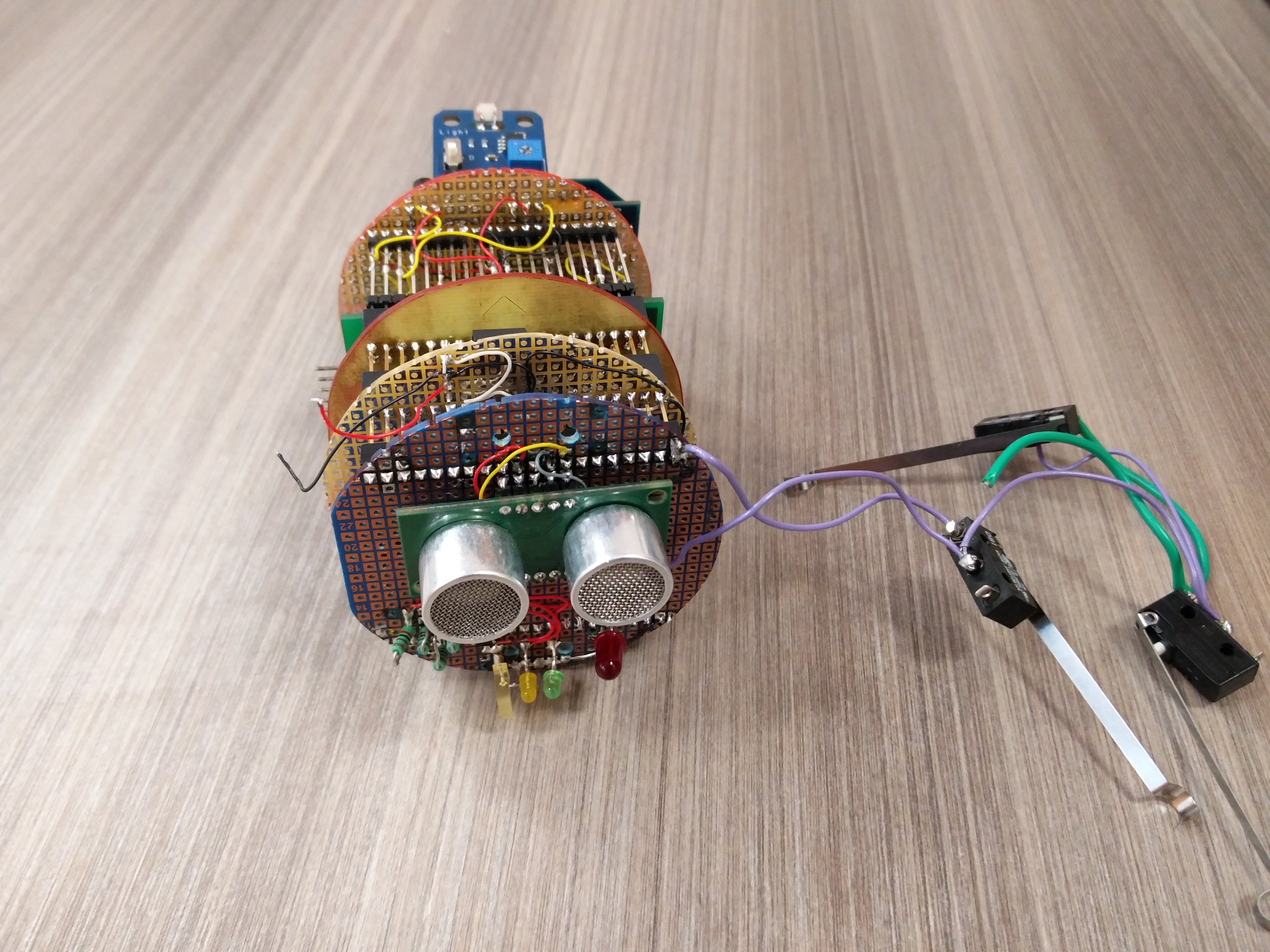
MEREDIEU-JUNG Clément BERTRAND Christopher DECKER-WURTZ Alexis
SOMMAIRE:
-
Définition Cansat
-
Cahier des charges:
–Missions
–Mesures
–Transmission des données
–Contraintes
-
Stratégie
-
Tests réalisés
-
Gestion des tâches
-
Réalisation de la mission libre
-
Fabrication physique de la CanSat
-
Prototype du parachute
-
Problèmes rencontrés
-
Avenir du projet
-
Vidéo présentation du projet
-
Remerciement
Définition Cansat:
Cansat est un concours qui met en compétition plusieurs écoles, le but étant de larguer des petits modules, du même nom, en altitude. La descente sera gérée par parachute. Arrivée au sol, la Cansat devra réaliser plusieurs missions et mesures.
Cahier des charges:
Notre but était de concevoir et de réaliser une Cansat à l’aide d’un PIC18F4520 (microcontrôleur). Ce module devra être équipé d’un parachute, à dimensionner selon le poids de la Cansat, afin de faire atterrir en douceur cette dernière sur le sol.
Nous avons dû réaliser plusieurs missions et différentes mesures à l’aide de capteurs. Ces missions et mesures sont détaillées ci-dessous.
Missions:
- Première mission: Nous devons indiquer à l’aide de leds de différentes couleurs les étapes de la phase de descente de la Cansat. Ces étapes représentent la distance entre le sol et la Cansat à trois mètres, un mètre et trente centimètres.
- Deuxième mission: Elle consiste à transmettre toutes les informations de la Cansat, à savoir toutes les mesures effectuées au sol ainsi que celles prisent lors la phase de descente.
- Troisième mission: Tenir 72h sur batterie, à savoir 4*1,5V, sans aucune alimentation externe.
- Quatrième mission: Nous avons décidé que l’objectif de cette mission sera de détacher le parachute afin qu’il ne fausse pas les mesures réalisées.
Mesures:
1. Mesure pendant la descente:
- Nous allons effectuer des mesures de distances entre le sol et la Cansat à différents seuils. Ces seuils sont à trois mètres, un mètre et trente centimètres.
- Nous utilisons un capteur ultrason pour effectuer ces trois mesures.
Caractéristiques:
Alimentation: 5 Vcc
Consommation: 30 mA
Portée: de 10 cm à 3 m
Déclenchement: impulsion TTL positive de 10µs
Signal écho: impulsion positive TTL proportionnelle à la distance.
Au début nous devions utiliser deux capteurs: un capteur d’ultrason (SRF04) et un capteur infrarouge (GP2D120). Cependant notre capteur infrarouge était défectueux et le capteur d’ultrason SFR04 n’avait pas une plage de mesure qui incluait tout nos seuils. C’est pourquoi nous avons décidé d’utiliser le capteur d’ultrason SFR05 qui lui peut effectuer toute les mesures dont nous avons besoin.
2. Mesure au sol:
- Comme expliqué précédemment ces mesures seront effectuées une fois que le module sera arrivé au sol.
- Capteur de température: LM35CAZ
Caractéristiques:
Indice de température : -40 à +110 °C
Précision : ±0,75 °C (typique)
Gain de la sonde (sortie) : 10 mV/°C
Faible auto-échauffement : 0,08 °C sans courant d’air
Tension d’alimentation : +4 à +30 V c.c.
- Capteur d’humidité: HIH-4000-003
Caractéristiques:
donne l’humidité en pourcentage
Précision : ±3.5%
Tension d’alimentation : 4 à 5,8 V c.c.
Température de fonctionnement : -40 à +85 °C
- Module capteur de lumière: Module capteur de lumière Electronic Brick
Le capteur de lumière va nous renseigner sur le niveau d’exposition à la lumière de la Cansat. On pourra savoir si la Cansat se trouve dans une pièce éclairée ou non par exemple.
Caractéristiques:
Consommation : 5mA
Alimentation : 5V
- Capteur de vibration: MEAS piezo
En prenant les valeurs brutes à la sortie du capteur nous avons créé différents seuils afin de détecter quand la CanSat est en déplacement , quand elle est posée sur une paillasse occupée ou non occupée (la CanSat sera entreposée dans une salle pendant les 72h de test).
Caractéristiques techniques:
Minimum d’impédance d’entrée : 1MΩ
Impédance recommandé : 10MΩ
Température de fonctionnement : -40 à 60°C
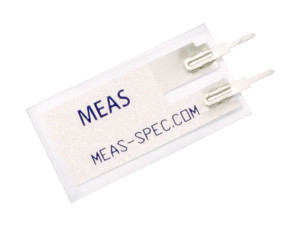
- Capteur de son: Parkfun Sound Dectector (SEN-12642 ROHS)
- Caractéristiques techniques:
Tension d’alimentation : 3.5 à 5.5 V (idéalement 5V)
Gain en dB : 40 à 28
Ce capteur peut être utilisé de trois manières différentes, grâce à trois sorties distinctes: audio, envelope, gate.
- La tracé vert foncé représente la sortie audio du capteur. La tension de la sortie audio est directement la tension fournie par le micro. Ce qui veut dire que le son capté par le micro est directement retransmit à la sortie audio.
- Le tracé vert clair représente la sortie envelope. Cette tension trace l’amplitude du son.
- Le tracé rouge représente la sortie gate. Elle est booléenne, dès qu’un son est détecté la sortie passe à un niveau logique haut.
Nous avons choisi d’utiliser la sortie envelope de ce capteur pour pouvoir créer différents seuils de mesure.
Transmission des données:
Transmission des données par deux Xbee pro s1 liaisons point à point.

Contraintes:
- Dimension des batteries imposées (tenir 72h sur 4*1,5V)
- Dimension de la Cansat imposée
- Poids (environ 350g)
- Choc à l’arrivée
- Récupération et/ou stockage des informations
- Transmissions des données
- Pas d’appendice avant le largage
- Mettre un interrupteur on/off
- Sécurité des personnes
- Dimensionnement du parachute
- Budget
Stratégie:
- Nous avons fait le choix de prendre des capteurs analogiques, cette solution nous à paru évidente car nous venons de voir le convertisseur analogique numérique sur le PIC18F4520 dans une de nos matières (Multi-tâches temps-réel).
- Nous avons décidé d’utiliser uniquement le capteur ultrason pour effectuer toutes les mesures.
- Concernant la programmation, nous utilisons plusieurs tâches dans le programme avec des priorités différentes.
- -Notre première tâche est une tâche d’initialisation.
- -La deuxième tâche sert à gérer la phase de descente de la Cansat, elle gère l’allumage des leds en fonction des différents seuils.
- -La troisième tâche est une tâche dans laquelle nous effectuerons les mesures des capteurs de température, humidité et luminosité.
- -La quatrième et dernière tâche envoie les mesures vers un hyper terminal via une liaison point à point grâce à deux Xbee pro s1.
- Pour économiser le plus de batterie possible, nous avons choisi de basculer le PIC en mode veille entre chaque séquence de mesure.
- Nous avions le choix entre transmettre et/ou stocker les informations. Notre choix à été de transmettre les informations de la Cansat toutes les 10min vers un hyper terminal
Tests réalisés:
- Transmission des données:
Nous avons testé la transmission des données via deux Xbee pro s1 avec adaptateur usb. L’un des Xbee est en transmission et l’autre en réception, ils sont tout les deux branchés sur une plaquette de test différente et éloigné d’environ un mètre. Nous avons envoyé un compteur de 1 à 9 avec une base de temps d’une seconde et nous avons constaté que, hormis un décalage d’une seconde la transmission s’opère sans aucun problème.
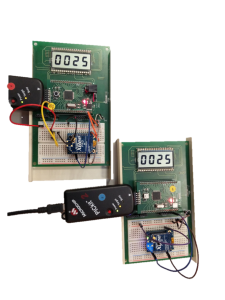
- Capteur de température:
Nous avons réussi à récupérer la mesure prise par le capteur de température puis nous l’avons traité via une formule pour la passer en degré Celsius. Cette opération est nécessaire sachant que le capteur renvoi une tension est non une valeur en degré Celsius.
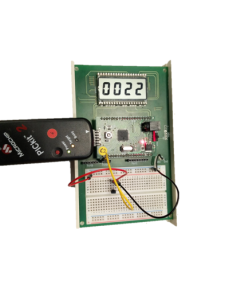
PICkit 2 branché à un PIC18F4520 qui récupère les information du capteur de température, les traitent puis les affichent sur l’afficheur LCD.
- Plaquette de gauche sur laquelle est branchée un PIC18F4520, un capteur de température et un module Xbee pro s1 en mode transmission ainsi qu’un écran LCD qui affiche la température mesurée à l’aide du capteur. La plaquette est alimentée par une batterie de 4*1,5V.
- Multimètre réglé en mode température et une sonde de température
- Plaquette de droite sur laquelle est branchée un Xbee pro s1 en mode réception et un afficheur LCD sur laquelle s’affiche la valeur reçu par le Xbee.
On constate dans cette vidéo que quand on souffle sur le capteur de température et la sonde de température simultanément, la valeur qui s’affiche sur l’écran LCD de la plaquette de gauche est la même que le multimètre une fois que ce dernier s’est stabilisé. L’écart entre les valeurs indiquées sur le multimètre avant qu’il ne se stabilise et l’afficheur LCD est dû à la grande inertie du capteur. On remarque aussi que la valeur affichée sur la plaquette de droite est la même que celle de la plaquette de gauche hormis un léger décalage dû au temps de transmission, donc on en conclut que la transmission est valide.
- Capteur d’humidité:
Le but est de mesurer et de transmettre via une plaquette de test puis d’afficher le pourcentage d’humidité sur l’afficheur LCD d’une autre plaquette.
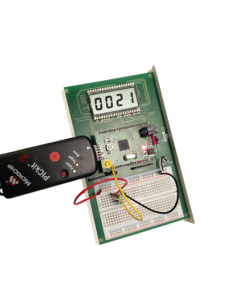
PICkit 2 branché à un PIC18F4520 qui récupère les informations du capteur d’humidité, les traitent puis les affichent sur l’afficheur LCD.
- Plaquette de gauche sur laquelle est branchée un PIC18F4520, un capteur d’humidité et un module Xbee pro s1 en mode transmission ainsi qu’un écran LCD qui affiche la température mesurée à l’aide du capteur. La plaquette est alimentée par une batterie de 4*1,5V.
- Plaquette de droite sur laquelle est branchée un PIC18F4520, un Xbee pro s1 en mode réception et un afficheur LCD sur laquelle s’affiche la valeur reçu par le Xbee.
Dans cette vidéo on voit que la valeur affichée sur l’afficheur LCD de la plaquette de droite est identique à la valeur sur l’écran LCD de la plaquette de gauche. On constate que quand on souffle dessus la valeur change et est envoyé via la transmission point à point des Xbee vers l’autre afficheur. On peut en conclure que la transmission est valide et que le capteur fonctionnne. On remarque néanmoins que les valeurs ne sont pas toujours les mêmes, cela est dû à l’inertie du capteur et au temps de transmission.
- Capteur de luminosité:
Notre but n’était pas de visualiser les valeurs en lux ou en lumen mais d’étalonner le capteur pour qu’il nous donne une indication sur le type d’éclairage de l’environnement où se trouve la Cansat. Pour l’étalonnage nous avons pris des mesures de référence à divers endroits: dans une pièce sans fenêtres et toutes lumières éteintes, dans une pièce avec lumières éteintes mais ayant l’éclairage de fenêtres, une pièce éclairée par des lumières, sous exposition à une lumière forte, et capteur couvert (à l’ombre d’un objet).
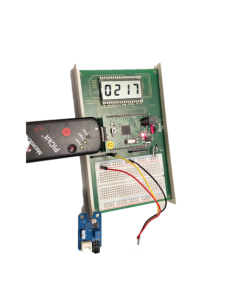
PICkit 2 branché à un PIC18F4520 qui récupère les informations du capteur de lumière, les traitent puis les affichent sur l’afficheur LCD.
- Plaquette avec PIC18F4520, afficheur LCD et module capteur de lumière.
On constate que quand on couvre le capteur la valeur diminue et quand on l’expose à la lumière la valeur augmente proportionnellement avec celle-ci.
- Capteur ultrason:
Nous avons décidé de faire des paliers avec les données brutes que le capteur nous envoi. Cela est plus simple et tout aussi efficace. Nous avons ensuite ajouté des indicateurs visuels(leds) afin de visualiser les différents paliers (3m,1m,30cm) et ainsi vérifier la précision de notre procédé. Nous avons aussi ajouté un capteur de contact afin de détecter atterrissage de la Cansat.
A trois mètres la led verte s’allume, à un mètre la led jaune s’allume et à trente centimètre la led rouge s’allume. Quand le capteur de contact est actionné, cela éteint toutes les leds et allume une autre leds rouge pour indiquer l’arriver au sol de la Cansat.
- Capteur de vibration:
Le capteur que nous avons décidé de faire par la suite est le capteur de vibration. Si ce projet avait pu aboutir jusqu’au concours, il aurait servi à savoir si la CanSat était déplacé, entouré par des gens ou même un tremblement de terre. Mais comme celle-ci restera entreposée dans une pièce, nous avons décidé de rentrer 3 seuils de détection: déplacement de la Cansat, paillasse occupée, paillasse non-occupée.
- Capteur de son:
Nous avons installé ce capteur afin de détecter si la salle est occupée ou non.
Sur ce programme nous envoyons la mesure de l’intensité sonore puis selon nos tests nous avons créé des seuils pour nous informer si la salle est occupée ou non.
Gestion de la descente:
- Tâche 0 : Tâche d’initialisation du pic18F4520.
- Tâche 1 : Cette tâche sert à gérer la phase de descente. On y retrouve le code permettant de piloter les leds représentant les différents seuils, ainsi que le code permettant d’effectuer les mesures avec le capteur d’ultrason.
- Tâche 2 : c’est la tâche réservé aux mesures des différents capteurs, qui sont tous analogique, ainsi que l’interprétation de ces mesures à la sortie du convertisseur analogique numérique(CAN).
- Tâche 3 : Elle sert uniquement au décrochage du parachute par l’action du servomoteur.
- Tâche 4 : C’est la tâche d’envoi des données. Par l’intermédiaire d’un Xbee nous envoyons, sur l’HyperTerminal de Windows, un affichage exposant clairement le nom des capteurs et les valeurs associées à ces capteurs ainsi que leurs interprétations.
Réalisation de la mission libre:
Rappel de la mission libre : décrochage du parachute avant l’atterrissage pour éviter de fausser les mesures si le parachute vient recouvrir la CanSat.
Pour cela nous utilisons un servomoteur: Anlog Servo de chez Makeblock.
Caractéristiques techniques:
- Tension 4.8 à 6V
- Couple 1.3 à 1.7 kg.cm
- 0.10 à 0.09 sec/60°
- 1000-2000 μsec
Pour réaliser cette mission nous avons intégré le servomoteur à la plaquette capteur de la CanSat. Nous avons ensuite ajouté deux axes sur le servomoteur qui partent de part et d’autre de la CanSat dans deux trous percés dans le tube en PVC afin de les bloquer pour pouvoir y accrocher les suspentes du parachute. C’est lors de la rotation du servomoteur que les axes vont sortir des trous et donc libérer les suspentes.
Fabrication physique de la CanSat:
Notre CanSat est constitué de quatre plaquettes, toutes ces plaquettes sont reliées par l’intermédiaire de stack qui assure à la fois la tenu mécanique de l’ensemble et permet aussi de faire transiter toutes les entrées/sorties/alimentation du microcontrôleur sur chaque plaquette. Le tout est contenu dans un tube en PVC.
- Première plaquette: Plaquette de mesure, transmission de donnée et largage de parachute. Cette plaquette inclus donc tous nos capteurs(température, humidité, luminosité, vibration et son), le Xbee permettant la transmission de donnée, le servomoteur permet le largage du parachute et un switch on/off.
- Deuxième plaquette: Plaquette sur laquelle se trouve la carte mère.
- Troisième plaquette: Plaquette d’alimentation comportant quatre piles AAA branchées en série, un régulateur LM7805 qui régule la tension à 5V.
- Quatrième plaquette: Plaquette de descente comportant le capteur d’ultrason, les leds représentants les différents seuils de la descente et les contacts pour détecter l’arrivé au sol.
Prototype du parachute:
- Dimensionnement du parachute:
Formule : (2*M*G)/(R0*Cx*V²)= Surface du parachute en m²
M : masse en gramme
G : 9,81 N/Kg
R0 : Masse volumique de l’air = 1,21
Cx : Coefficient de pénétration dans l’air = 1
V : vitesse en m/s
Nous avons trouvé une surface de 0,68m², donc un rayon de 46cm et donc un diamètre de 92cm.
Pour le prototype du parachute nous nous sommes servis d’un sac poubelle à défaut d’avoir une vraie toile.
Test réalisé à l’aide d’une bouteille d’eau avec une masse d’environ 350g pour modéliser le poids de la CanSat.
Ce test a été concluant, nous avons pu observer que le parachute ralentissait assez le poids fixé pour un atterrissage en douceur.
Problèmes rencontrés:
- Vérifier la fonctionnalité de nos capteurs, car ils ont déjà été utilisés.
- Chercher et trouver les bonnes datasheets et les formules de conversions des composants.
- Le voltage des piles en mode embarqué qui été trop faible (inférieur à 4V) pour faire fonctionner les composants. Nous devions modifier les calculs afin d’intégrer le bon voltage quand les batteries étaient supérieures à 4V et donc utilisables, car quand la plaquette est branchée sur le PICkit 2 celui-ci délivre 4,80V.
- La compatibilité et la protection des ressources lorsque nous avons réuni plusieurs programmes en un seul et même programme.
- Gestion du temps: nous avons passé trop de temps sur la réalisation des programmes et pas assez sur la réalisation physique de la CanSat.
- Non respect de la contrainte de volume , la CanSat est trop grande.
Avenir du projet:
- Rechercher comment utiliser le mode veille du PIC18F4520 pour économiser les batteries.
- Couper l’alimentation des capteurs entres chaque mesures à l’aide d’un transistor afin d’économiser les batteries.
- Couper l’alimentation du servomoteur et de la plaquette descente (ultrason et leds) à l’aide d’un transistor afin d’économiser les batteries, une fois la CanSat arrivé au sol.
- Fabrication du parachute en toile.
Vidéo présentation du projet:
Remerciement:
Nous tenons à remercier Mr HAEBERLE, Mr VERRIER et nos collègues du projet Cansat IR.